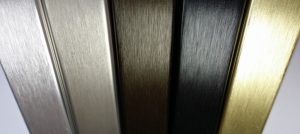
Anodising is an electrolytic process that applies an oxide film on aluminium. This film increases the metals naturally good corrosion resistance, and protects any polishing, linishing, etching or brightening. An attractive characteristic of anodising is that colour can be incorporated into the oxide film during the process of anodising or immediately after it.
The basic stages of anodising are:
Pre-Treatment – The ultimate surface texture required will determine the type of pre-treatment necessary. This can either be mechanical, (polished, linished, etc) or chemical (etched, chemically brightened, etc).
Anodising – Anodising involves passing an electric current through a sulphuric acid electrolyte with the aluminium work piece as the anode. The thickness of the anodic film produced is proportional both to the current passed and the time the aluminium is treated, and generally ranges from 3 micrometres (also known as “microns”) up to 25 micrometres.
Colouring – After anodising the anodic film is porous and is capable of absorbing dyes, pigments and other compounds that induce a coloured finish.
Sealing – The pores of the anodic film are sealed by hydration in boiling water or chemical solution, as the final stage in the process.
Jigging Points – In order to minimise irregularities in film thickness it is essential to provide a firm electrical contact between the jig bar and the work being anodised. Where possible these jig marks, with no protective film or colour, are kept to non-significant faces. If all faces are visible it is important to discuss at an early stage at which points jig marks will be acceptable.
For further information and criteria please click here to see our Clauses pages.